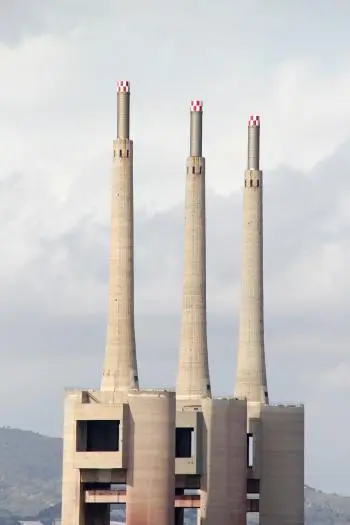
Ein Wärmekraftwerk ist ein elektrisches Kraftwerk, das Wärmeenergie in elektrische Energie umwandelt. Der Unterschied zwischen einer Pflanzenart und einer anderen besteht in der Art und Weise, wie die Wärme gewonnen wird.
Die Wärmequellen eines Wärmekraftwerks sind:
- Fossile Brennstoffe (Kohle, Diesel und Erdgas)
- Kernreaktionen von Uranatomen.
- Biomasse.
- Solarenergie.
Die ersten beiden sind nicht erneuerbare Energiequellen. Andererseits gelten Biomasse und Solarenergie als erneuerbare Energie, obwohl erstere Treibhausgase emittiert und solarthermische Kraftwerke dies nicht tun.
Wie funktioniert ein konventionelles Wärmekraftwerk?
Ein konventionelles Wärmekraftwerk ist ein thermoelektrisches Kraftwerk, das Kohle, Öl oder Erdgas als Brennstoff verwenden kann. Trotz der Umweltbelastung und des Ausstoßes von Kohlendioxid und anderen Treibhausgasen sind sie die am weitesten verbreiteten Wärmekraftwerke.
Die Funktionsweise des Kreislaufs konventioneller thermoelektrischer Kraftwerke ist unabhängig von der Art der Wärmegewinnung gleich.
Das typische Wärmekraftwerk ist in mehrere Segmente unterteilt: einen Kessel, eine Turbine, einen Generator und einen Kondensator.
Im Kessel wird der Brennstoff verbrannt, um Wärmeenergie zu gewinnen. Mit dieser Energie wird eine Flüssigkeit erhitzt, um Wasserdampf zu gewinnen. Dampf wird auf diese Weise zum Antrieb einer Dampfturbine verwendet, die innere Energie des Dampfes wird in mechanische Energie umgewandelt.
Schließlich ist die Dampfturbine mit einem Generator verbunden, der die Energie in Strom umwandelt. Der resultierende Dampf strömt durch einen Kondensator, um den Zyklus neu zu starten.
Was sind GuD-Kraftwerke?
Thermische Kombikraftwerke sind thermoelektrische Kraftwerke, die konventionelle Kreislaufkraftwerke mit einer Gasturbine kombinieren. Die kombinierte Nutzung von Gas- und Dampfkreisläufen verbessert die Energieeffizienz und es werden Ausbeuten nahe 55 % erzielt.
Als Brennstoff für diesen Anlagentyp dienen Erdgas, Diesel und bei spezieller Aufbereitung sogar Kohle.
Das Hauptmerkmal des Gaskreislaufs ist, dass es keine Phasenänderung des Fluids gibt. Der Ablauf ist folgender:
- Gaskompression.
- Gasheizung.
- Gasexpansion in einer Gasturbine. In diesem Fall ist die Turbine mit einem elektrischen Generator verbunden, um Strom zu erzeugen.
Das aus der Gasturbine austretende Gas hat noch eine sehr hohe Temperatur, so dass es zur Dampferzeugung und parallel zur Aktivierung eines konventionellen Kreislaufs verwendet wird.
Können Wärmekraftwerke mit Sonnenenergie betrieben werden?
Solaranlagen können mit Sonnenenergie betrieben werden. In diesem Fall werden Sonnenkollektoren auf einer großen Fläche platziert, die Spiegel sind, die die Sonnenstrahlung auf denselben Punkt lenken.
Die Konzentration der gesamten Sonnenenergie an dieser Stelle erzeugt sehr hohe Temperaturen, die zur Dampferzeugung genutzt werden.
Ab hier ist der Betrieb wie in jedem konventionellen Wärmekraftwerk.
Welche Auswirkungen haben thermische Kraftwerke auf die Umwelt?
Wärmekraftwerke, die fossile Brennstoffe nutzen, erzeugen Kohlendioxid und andere Treibhausgase. Überschüssige Gase in der Atmosphäre sind sehr schädlich, weil sie die globale Erwärmung des Planeten begünstigen.
Derzeit sind thermoelektrische Kraftwerke verpflichtet, ihre Emissionen zu kontrollieren. Diese Verpflichtung ist insbesondere für Großkraftwerke relevant, bei denen es einen wichtigen Abschnitt zur Schadstoffreduzierung gibt.